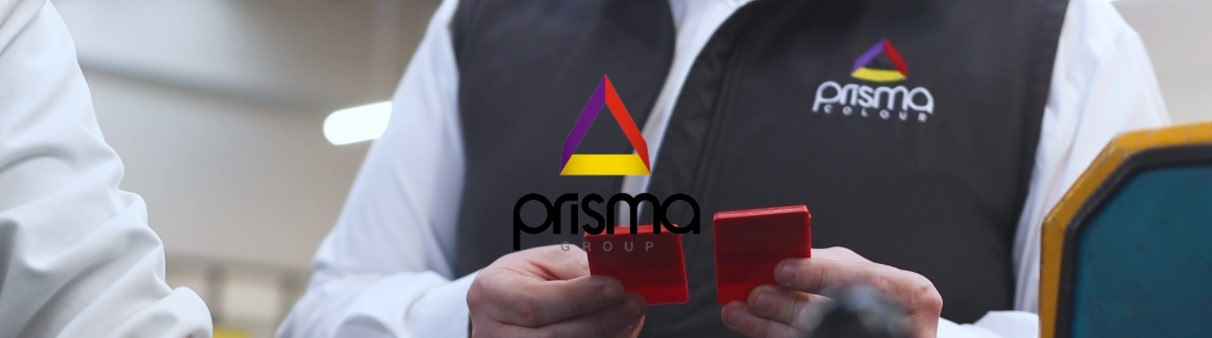
With such diversity in the polymer processing industry regarding; processes, base polymers, and end user applications, it is essential to grasp the customers’ needs to design the product to exact requirements. It is therefore of fundamental importance when formulating a colour match first time, that you have all the information relevant to the specific end product, and the process in which it will be going through, when considering which pigment or dyes to use.
Quite often in the industry, a masterbatch or colour masterbatch manufacturer will be asked to match to a colour coating on card or paper (we know which ones we are talking about!) Many colour swatch books, should only ever be used as a guide to an end colour requirement. They are printed using pigment systems that may not be necessarily suitable for the plastic and rubber industries. For example, they may be more appropriate for inks or coatings.Example of the same colour between 2 swatch booklets.
Another key problem with the dependence of swatch booklets is the difference in age and upkeep of the swatches themselves. The paper and coating can fade with light and UV exposure, resulting in an inaccurate representation of the standard.
These are problems because:
- Colourant formulations are often complex in order to meet the varied requirements of the players in the supply chain and all pigments and dyestuffs are not suitable to meet these end requirements
- There is a multitude of colourants on the market and all of these will not possess the correct colouristics, such as hue, brightness, or strength to arrive at the end colour standard.
- Most bases require different pigments in order to design the product to the specifications of the end applications.
Three swatch references of the same colour
Failing to gain all the necessary information from the customer and proceeding with an inaccurate standard, may have serious consequences for all businesses within the supply chain. The customer may not receive the correct product and incur costs as a result. The supplier can produce incorrect product and acquire the costs of remanufacturing. This could even cost pigment suppliers earlier in the supply chain, handling with incorrect orders.
At Prisma Colour, we work with your business to ensure misunderstandings like this, don’t happen. Our communication is key to the way we operate; therefore, we will consult with you to ensure we design a product that incorporates all the specifications required for your end application.
Have you seen these issues with your supply?
Contact Us now to enhance your formulations and further improve your colour match accuracy!
Recent Comments